TempRite® Engineered Materials’ CPVC resins are characteristically strong, resistant to heat and corrosion and retain their toughness over a long period of time. However, its true usefulness is in the application of CPVC to compounds, giving their increased flexibility and safety qualities in hazardous environments. Electrical applications are a perfect example of this.
Manufacturers of electrical power distribution tools and fixtures look to thermoplastics for their mechanical and insulation qualities. It is used in the manufacture of trunking and conduits, cabling, housing and much more. A high-performance thermoplastic guarantees safer power distribution, flexible installation and a professional finish.
This is why TempRite CPVC is a strong choice. It is fundamentally engineered for flexibility of strength in compounds and adds an additional layer of safety, to adhere to even the most stringent industrial standards:
- Flash Ignition Temperature
- Limiting Oxygen Index
- Flame Retardancy
Engineering CPVC’s Performance
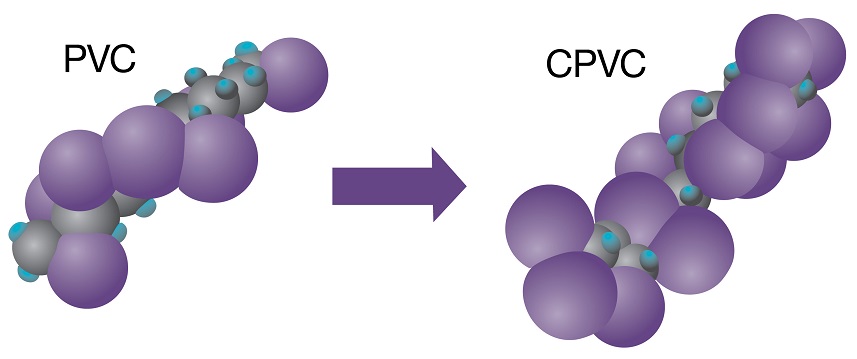
A typical CPVC compound used in electrical product manufacturing consists of CPVC resins, and countless optional additives to help augment its performance characteristics. However, it is in the resin itself that CPVC achieves such high fire and heat resistance, thanks to the additional layer of chlorine atoms that are added during the chlorination of PVC to make CPVC.
Flash Ignition Temperature
This chlorination process allows CPVC to reach much higher temperatures before it eventually breaks down and releases free radicals, causing it to ignite (Flash Ignition Temperature.) At 482℃, its closest rival in thermoplastics is rigid PVC, at 399℃.
Limiting Oxygen Index
Combustion characteristics indicate that under normal conditions, CPVC in electrical installations would likely be incapable of burning.
TempRite CPVC has a high Limiting Oxygen Index of 60. This means that in order for CPVC to burn, there would have to be 60% oxygen in the air. Earth’s atmosphere contains just 21% oxygen. If a flame was constantly applied to CPVC, it would burn; however, burning would cease the moment the flame is removed.
Fire Rating
Fire rating requirements in electrical applications are increasingly stringent. CPVC is required to attain a rating of BS3 or BS2 as an absolute minimum, in accordance with European Fire Classification EN13501. TempRite CPVC has a fire rating of BS1D0, the highest rating a plastic can achieve.
RTI
The Relative Temperature Index is relative to thermal degradation of materials, and a very high RTI rating is required. However, this is where PVC has limitations. Unmodified CPVC has a high rating on its own, before adding flame retardants for increased fire safety. The standard accepted RTI is 80 degrees; CPVC’s RTI is 105 degrees plus (depending on the compound.)
UL94
This is the flammability standard, recognised and required in both Europe and the US. It is measured based on 6 classifications of how plastics burn in different environments.
CPVC has a UL94 rating of V-0 (burning stops within 10 seconds on a vertical part allowing for drops of plastic that are not in flames.) PVC’s average rating is V-1 or V2, depending on the formulation and needs additives to achieve V-0.
The accolades achieved by CPVC’s base resin alone automatically render future compounds more efficient and safe; a sensible and cost-effective choice for electrical engineering.
WEEE Compliance
In accordance with WEEE, (Waste Electrical and Electronic Equipment), CPVC does not require excessive use of these listed chemicals:
- Lead
- Mercury
- Cadmium
- Hexavalent chromium
- Brominated flame retardants
- Bis(2-Ethylhexyl) phthalate (DEHP)
- Benzyl butyl phthalate (BBP)
- Dibutyl phthalate (DBP)
- Diisobutyl phthalate (DIBP)
Its chlorine structure provides natural flame retardancy for safety, without the need for hazardous additives, allowing it to be used more freely in electrical applications.
CPVC Resistance in Electrical Environments
CPVC is resistant against Sulfur Oxide (SOx) and Nitrogen Oxide gases (NOx); such pollutants are common in industrial environments that require a lot of power. NOx and volatile organic compounds can also produce ozone, a highly corrosive pollutant which CPVC successfully defends against.
Better Processing With CPVC
TempRite Engineered Materials have engineered specially developed compounds for custom injection moulding and profile extrusion. The materials we have developed are easy to process for tooling and downstream equipment during the extrusion process.
These materials can be used in a similar way to PVC; however, melting temperatures and processing windows are very similar to that of CPVC.
This makes it easier for product engineers who use PVC to begin using CPVC and experience the benefits.
Blending Polymers for Electrical Applications
Many electrical installations can improve their mechanical strength, resistance to heat and fire safety ratings when their thermoplastic compounds are blended with CPVC. A popular blend for electrical profiles is CPVC and PVC.
There are many reasons why product designers might blend the two polymers together:
- Easy Processing of PVC/CPVC for injection molding and profile extrusion
- To improve resistance - creating CPVC/PVC blends to improve heat/fire/flame resistance
- To improve performance - a 50/50 or 60/40 blend of CPVC/PVC will achieve a fire rating of BS2D0 (you need to push CPVC over 70% in blend to achieve BS1D0.)
Popular Electrical Applications of CPVC
Electrical Busbars
For local high current power distribution, electrical busbars require reliable trunking for maintaining a safe environment 24 hours a day. Trunking for these high-power metallic strips of conducting material are typically injection moulded; CPVC acts as a strong outer shell and insulator and is suitable for injection moulding.
Recent tests have included using a blend to push the UL94 V0 rating, by adding CPVC. Initial testing has been very promising so far, a good indicator of even safer high power electrical distribution in the future.
Track Lighting Fittings
CPVC is often used in track lighting - racks affixed to ceilings where light fixtures are installed. Tracks contain electrical conductors and are a popular choice for installers who want to embed lighting into the ceiling. Thermoplastic is naturally a preferred choice for the safe distribution of power; CPVC’s high softening temperature allows strong track lighting to be extruded at 115℃.
Electrical Conduits
Flexible and strong conduit material must be used to protect and route electrical wiring. CPVC is used effectively in this application, ideally with PVC, adding mechanical stability. Fire behaviour is also closely regulated; CPVC’s compliance with EN13501 to the highest possible level for plastic achieves this. In the event of fire, CPVC natural self-extinguishing properties prevent any further spread.
As standards for safety and efficiency perpetually evolve and increase over the years, as does the performance of thermoplastics when blended with TempRite CPVC. For hazardous environments where electrical distribution powers businesses, communities or even nations, a strong, stable and safe performance is everything.