TempRite® Engineered Materials’ development of CPVC with inherent resistance to heat has allowed product engineers to push the limits of what ordinary objects can do. Compounds produced from CPVC resin can be applied in indoor and outdoor environments where other plastics become susceptible to degradation.
Heat-Related Strengths
These are just some of CPVC’s inherent heat-related strengths:
- Higher softening temperature
- Flame and smoke performance
- Acid and oxidiser resistance
- Thermoformability
- Impact resistance
- Flexibility
How TempRite® CPVC Achieves Heat Resistance
The CPVC polymer is produced by subjecting PVC to a chlorination reaction. Chlorine atoms occupy a much larger area of the materials’ carbon backbone. This stiffens the molecule and gives it a much higher softening temperature.
The bulky chlorine atoms also serve to protect the carbon chain of the polymer from oxidative attack and stabilize it against chain cleavage reactions.
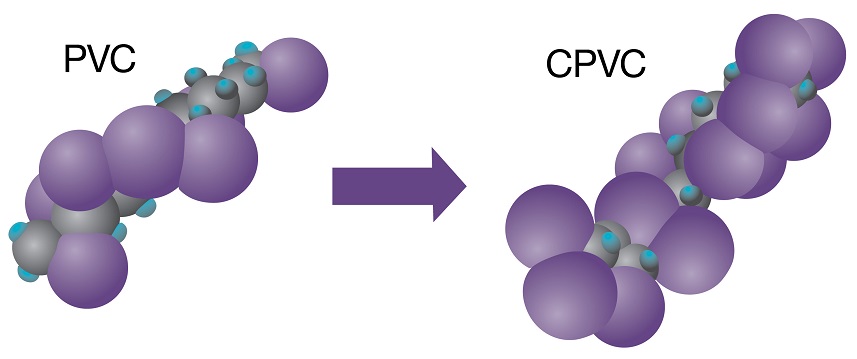
Due to this inherent strength and stability in the polymer itself, any resulting compound starts off strong, with many heat-related advantages at the outset.
Flexibility of Heat Resistance
Because CPVC is made with a post-chlorination reaction, TempRite Engineered Materials can produce CPVC resins with various levels of chlorine content and molecular weight. This allows for flexibility in terms of heat resistance. The inherent heat resistance in CPVC can therefore be scaled up or scaled-down. However, the higher the molecular weight and chlorine content, the harder CPVC is to process.
CPVC compounds are rarely processed without additives. Typically, a CPVC compound consists of 85% resin and 15% additives - this 15% can either boost or limit CPVC’s inherent heat-related strengths.
Typical CPVC additives include:
- Stabilizers
- Antioxidants
- Impact modifiers
- Processing aids
- Lubricants
- Pigments
For product designers, the scalability of CPVC’s heat resistant qualities offers a new level of flexibility in manufacturing. This gives engineers the technical and financial advantage in the creation of new products.
Applying CPVC Outdoors
It is often assumed that thermoplastics cannot withstand harsh outdoor environments, where temperatures can soar to exceptionally high levels in the summer and UV rays generate destructive free radicals. However, TempRite CPVC’s UV resistance is inherent. You would not be able to produce CPVC polymers without it.
In the same way CPVC’s molecular structure is built to withstand heat-related incidents such as oxidation, CPVC’s UV resistance also protects against free radicals. Typically, UV splits molecules to make free radicals which can cause adverse reactions such as chain cleavage. CPVC has exceptional resistance to this well known form of plastic degradation. CPVC is actually produced in an environment of intense UV light and free radicals without any significant reduction in its molecular weight.
This enables manufacturers to rethink where plastic can be applied cost-effectively, where end users typically rely on wood, stone or metal. For example, outdoor fencing and cladding can be produced in CPVC, with the aesthetic of natural wood or metal.
Temperature Limits for CPVC Applications
Amorphous polymers, such as PVC and CPVC have a high glass transition temperature (the temperature range in which a polymer changes from rigid to flexible). However as temperature decreases, CPVC retains its strength.
Semi-crystalline polymers such as PPR and PVDF can only be used above their glass transition temperature, providing less versatility.
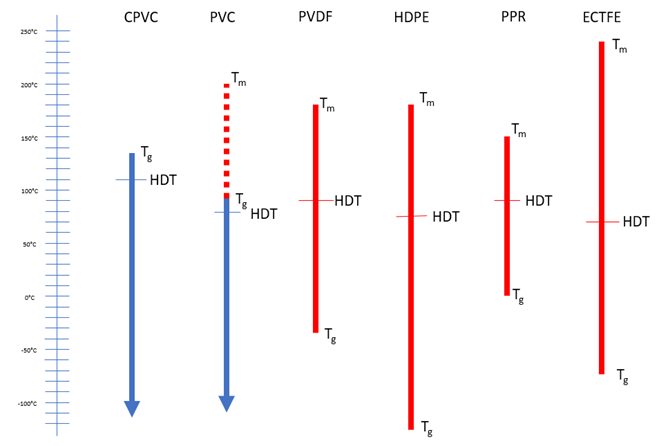
As a result, CPVC is being used in outdoor applications where temperatures reach far below freezing, such as piping material in Siberia.
Heat Resistance in Product Development
TempRite CPVC resins can perform effectively in compounds tailored for very niche products:
Foamed Paneling - Movable walls and partitions can be installed in temporary working spaces with the fire resistant benefits of CPVC to make the environment safer.
Foamed pipe - This is useful for drain waste and vent piping, often made with a foamed core which is solid on the outside, providing a lighter weight product for ease of installation.
Outdoor Panel Extrusion - CPVC paneling with an embossed or gloss finish on the outside provides designers with flexibility whilst losing none of the polymer’s core benefits.
Designers can fully develop a finished product with heat resistant qualities from the outset, without losing any aesthetic benefits. TempRite CPVC can create ordinary products that perform to an extraordinary level.